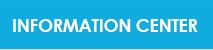
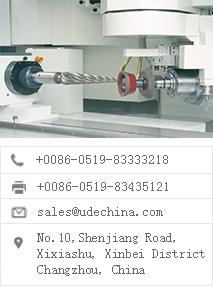
First, deep hole drilling cutter material selection attention problems
Tooth material should be based on each tooth load and cutting state suffered to choose. Center Tooth large axial force, friction extrusion serious, severe cutting conditions, it should be considered selection of high flexural strength, impact resistance, good YG class or YW class carbide blade; outer and middle teeth due to tooth cutting speed is higher, should be used in good red hardness, high wear resistance alloy YT, guide block should be used in high wear resistance YT-like material.
Second, deep hole drilling tool angle chosen attention problems
Deep processing tool based primarily on the angle of the workpiece material to be. Reasonable tool angle to ensure the stability of the drilling process, the breaker and improve tool life of great help. Rake angle and rear corner is one of the most important point of view, generally cutting edge of each front corner γ0 = 00, difficult materials to take γ0 = 1 ~ 30, workability good material take γ0 = 3 ~ 60, and the chill of brittleness desirable material negative; after the outer edge angle generally take α0 = 8 ~ 120, the inner edge should be bigger, take α0 = 12 ~ 150.
Third, pay attention to the problem tooth size selection
Cutter specifications are based on the process of cutting each cutting tooth is exposed to the choice of load conditions, while cutting load and tooth width related to tooth width should be distributed according to the size of each tooth cutting state and drill diameter. Tooth width allocation should meet three conditions:
1, A + C + e + F> d0 / 2 + (1 ~ 2) mm, i.e., the cutter teeth must exist a certain amount of overlap.
2, to ensure that the drill tip eccentricity e = (0.1 ~ 0.2) d0, e value of the material to be machined and drill diameter related to its size determines the size and direction of the radial force of the drill. A reasonable amount of eccentricity to make moderate radial beat machined hole wall, stabilizing drilling, guide and strengthen the role of improving the surface quality of the hole. While avoiding the drill point zero cutting, improving poor terrible at cutting conditions.
3, A + CeF> (1 ~ 3) mm, which allows the cutting radial force is always pressed against the guide block, the guide block against the forward wall of the machined hole, full use of the guiding action of the guide block, to ensure borehole straightness.
Tools Co., Ltd. Changzhou good to Main deep hole drilling, step drills, drills, reamers and other tools, welcome to buy!
- High-end manufacturing escort "M
- Characteristic Analysis of Stain
- Broad market of artificial intel
- Changzhou high performance milli
- Speeding up the Improvement of I
- Analysis of the Characteristics
- Made in China from "usable" to "
- Very good high-performance milli
- China 's new offshore oil seismi
- What are the precautions for the
- Dill |
- End Mill |
- Reamer |
- Special To...|
- TAPS Serie...|
- Machining |

联系人:薛小姐 138 6101 6292,付小姐 153 1256 7839